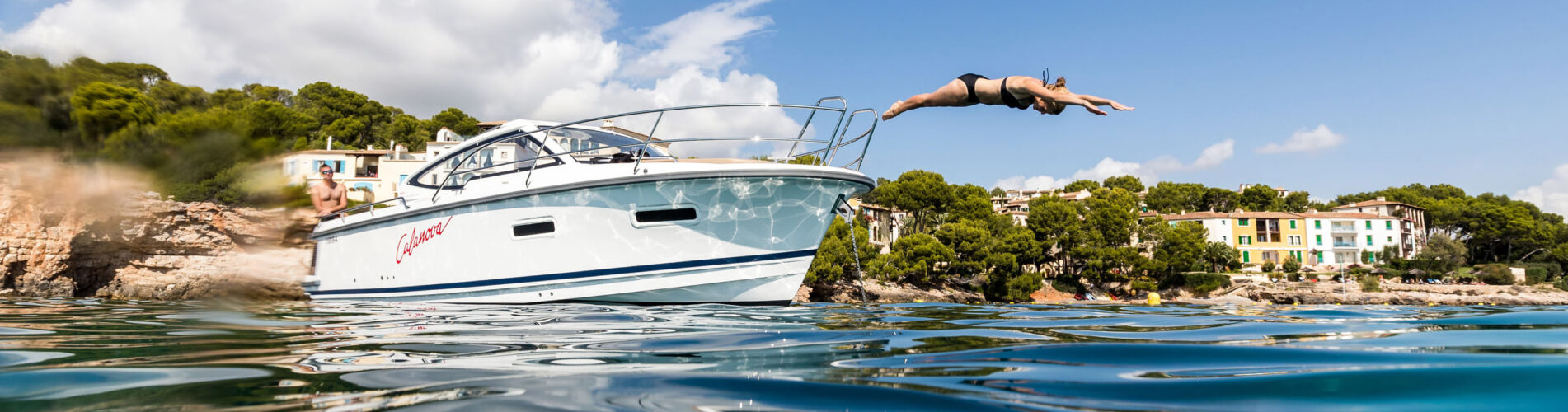
Marine Hardware
【Technical Blog】Process flow of marine propeller
【Technical Blog】Process flow of marine propeller
A perfect marine propeller will be finished as the following steps:
① Molding
② Casting metal
③ Blank processing
④ Finished product inspection
⑤ Installation and use
Molding
The pitch plate is used to scrape the spiral surface when making the lower sand mold, and its accuracy directly affects the manufacturing quality of the paddle.
Determining the dimensions of the pitch plate requires not only consideration of the pitch of the blade, but also the shrinkage of the casting material after pouring, the thickness of the brick table and the geometric characteristics of the propeller itself.
1) Calculation of equal pitch propeller pitch plate
The position of the pitch plate should be determined in this way: in addition to the blade radius R in the radial direction, the machining allowance a of the blade tip edge and the thickness b of the brick table supporting the sand mold in the future should also be considered.
At the same time, radial shrinkage of the metal should also be considered. In this way, the radius of the pitch plate should be (1+K)R+a+b; its circumferential position should be such that the fan-shaped area formed by the pitch plate and the center of the paddle can shield the orthographic projection area of the blade and leave a certain frame.
Let the arc length of the pitch plate be l, so the essence of finding the pitch plate is to find the arc length and the displacement of the generatrix in the axial direction.
2) Calculation of variable pitch propeller pitch plate
There are currently two forms of variable pitch, one is linear variable pitch, and the other is nonlinear variable pitch. The former requires only two pitch plates. The pitch at the tip is called the outer pitch plate, and the inner one is called the inner pitch plate.
The latter, in addition to the outer pitch plate, also requires a number of inner pitch plates, depending on the size of the propeller and the required accuracy.
Mold making
The propeller casting mold is generally a box-type sand mold, and the parting surface is a blade page. The pages are in the lower sandbox, and the leaves are back in the upper sandbox.
When making plastics in the lower sand box, first complete the appropriate cylindrical surface of the triangular pitch plate, and then use the scraper to scrape the spiral surface of the page by collecting the inclined edges of the pitch plate along the axis.
For the equal-pitch blades, only one scraper is needed, and a pair of scrapers are needed for the parts of the radial linear variable-pitch blades that change according to the pitch.
Rough casting
There are two casting methods for metal propellers: top casting and bottom casting.
Top casting method: The top casting method is to inject molten metal directly into the mold cavity from above the riser.
The advantage of this method is that the casting mold is simple, the operation is convenient, the temperature distribution is relatively reasonable when the metal is cast, the condensation has a certain direction, the riser temperature is higher, and the casting can be well compensated.
However, the oxides on the metal surface enter the casting together with the metal during casting, especially when the metal flows down, it generates splashes, is involved in air bubbles and impurities, and forms loose and scab on the surface of the casting to a certain depth, which affects the mechanical strength of the blade.
Therefore, it is only used for casting small (less than 1 meter in diameter) propellers.
Bottom casting method: It is to introduce metal liquid at the lowest point of the mold cavity, that is, the lower end of the propeller hub, in order to prevent common shortcomings such as oxides and shrinkage phenomena occurring at the back of the blade during casting.
Propeller processing
Process: cutting off the gate, riser, the processing of the two end surfaces of the hub and the shaft hole, inserting the key way in the shaft hole, scraping the shaft hole, processing the page and back of the blade, etc., for a balance experiment.
When processing, first cut off the riser, gate and other redundant parts at both ends of the hub, resulting in two reference surfaces at the front and rear of the hub, and then boring along the center of the hub and inserting the key way into the shaft hole.
Boring can be performed on a lathe or boring machine. Some large paddles can also be processed with homemade vertical or horizontal boring rows. Generally, a template or axis is prepared to check the processing quality.
Blade processing
According to the blade outline drawn by the propeller measurement, the extra parts are cut out in batches, and then the blade surface and blade back are processed.
The processing of the leaf back is based on the leaf surface.
After the blade surface is processed, use it as a reference surface to re-measure the thickness of the blade, and determine the thickness of the metal layer to be removed from the back of the blade according to the requirements of the drawing. Drill first, and the drilling depth is the thickness of the processed metal layer.
For the depth of the hole, scoop out the shape curve of each section and then remove the excess metal layer along the radial direction of the blade.
What material make a perfect marine propeller?
Propeller materials are usually copper alloy, cast iron and cast steel, but with the development of science and technology, many new materials, such as fiberglass and nylon, have also become one of the propeller production materials. Propeller materials require sufficient mechanical properties. It also needs to be compatible with multiple metal chemical properties.
As a commonly used spiral sword material, manganese bronze has the characteristics of large elongation, good impact resistance and corrosion resistance. This material is often used in the manufacture of propellers for marine ships. However, this material has poor erosion performance.
Aluminum bronze is a kind of Multi-alloy with copper-aluminum alloy as the main body. It adds manganese, iron, nickel and other elements on the basis of copper and aluminum. In addition to its advantages of manganese bronze, its weight and fatigue are relatively compared. Low, so many large high-speed ship propellers use it as the main material. Its disadvantage is that the technical requirements for smelting and pouring are relatively high. At the same time, the problems of cold brittleness of large castings are difficult to deal with and expensive.
Cast iron propellers have low cost and easy casting, so they are widely used in small ships. However, due to low mechanical strength, brittleness and fragility, and easy to be corroded by seawater, the service life is short. At the same time, its own section thickness ambassador's operating efficiency of the propeller is reduced, so it can only be used on small low-speed ships.
The mechanical properties and impact resistance of cast steel propellers are very strong, but their casting process is uniformly deformed, which makes the propellers deviate from the actual size after processing. At the same time, cast steel is more susceptible to seawater erosion than other metals, plus
The service life is short, so the scope of application is very small, and only the nickel alloy, titanium alloy, etc. will be used to make the cavitation erosion.
The following picture will show you what type of the raw material we are using for marine propellers
previous :
Caring for marine seacock valvenext :
Copper JIS Specificationscategories
recent posts
copyright © 2025 XIANG YI INTERNATIONAL LTD..all rights reserved. powered by dyyseo.com
ipv6 network supported
friendly links :
Marine Lifesaving Equipment